製造業のムダ取り:作業の設計をして、ムダを検出する(工場のラインキーパーの例)
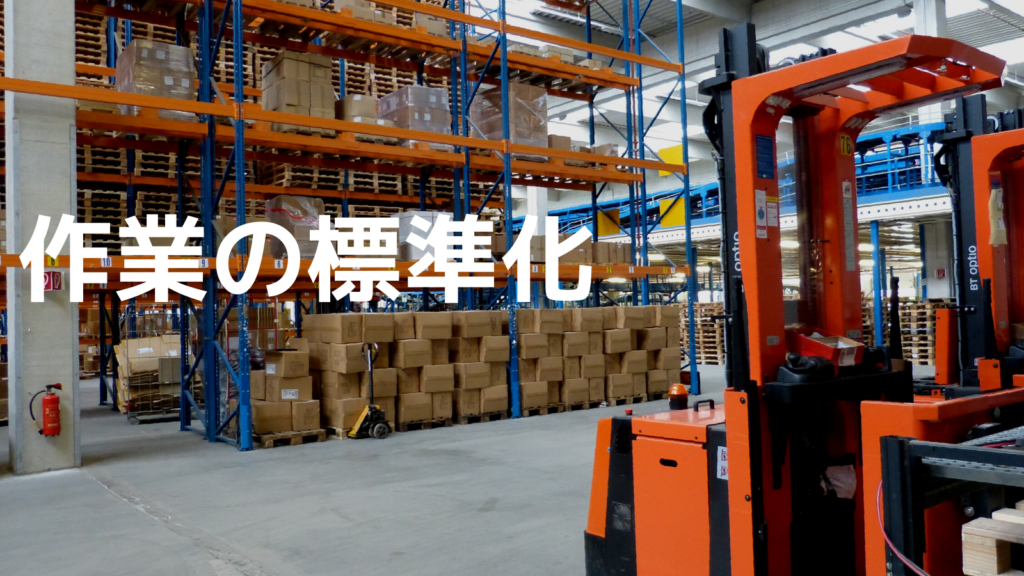
もう20数年前のことだろう。
名の知れた会社に診断で訪問すると、最初に、会議室で明快に、会社概要や方針・目標、取り組みについて説明していただきました。「さすが、さすが」です。そして、現場へ。
すると、先ほどの資料の説明とは異なった印象を持ちました。
現場に方針・目標が伝わっていない。
設備中心の現場は、TPMに力を入れているものの、一方、ひとの動きには、目がやりきれていない。これを察知した私は、現場リーダーに、ある作業者を指し、「あの方の動きに余裕やムダはありませんか?」こんな問いをしました。
その回答は、
「いつ見ても、忙し気に動いています。とても余裕なんてありません」
現場の作業には、余裕やムダが見えやすい対象とそうでない対象があります。一般的に、特定の場所で、短サイクルの繰り返しの作業は、見えやすい典型です。
一方、目の届かない範囲を動き、サイクリックでない作業は、見えにくい典型と言って良いでしょう。今、問うた方は、正に、この見えにくい対象と見てとれた作業者です。この方の仕事は、充填ラインに必要な梱包材や添付品を供給し、空になった箱を回収するといった仕事です。
仕事の指示内容を聞くと「ラインを止まらせないように、梱包材と添付品の供給、及び空箱の回収をしてください」とされています。
この指示の仕方(作業の単位/順番、時間などの指示無し)からも、ますます余裕やムダが内在している懸念が伺えてきます。
作業者の1日の動きを聞くと、
- ライン稼働後、翌日分の梱包材や添付品の入った段ボールを製造フロアーに運搬
- 空いている時間に、少しづつでも作業を進める。開梱して保管場所をずらす。
- ラインが止まらないように、ラインサイドへ供給
- ついでに、空箱回収と片付け
とのこと。
また、その範囲の現場を観察していくと、ラインサイドまでの間に点在する仕掛状態の段ボールが観察されます。その姿からは、少しづつ作業を進めようとする作業者の使命感や責任感が伺えます。しかしながら、良かれと思ってしている作業の方法が、2度手間や余計な仕掛状態を生じさせていることも多いものです。
ではでは、ということで、質問と観察を続けます。
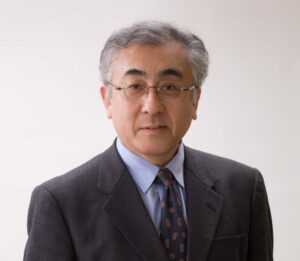
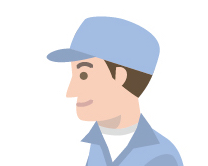
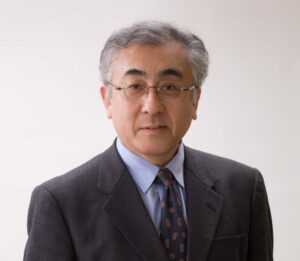
①3箱づつ段ボールをラインサイドへ運搬
②3箱づつ空箱を回収、整理
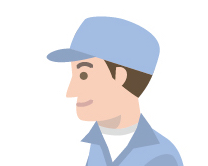
・・・やってみる
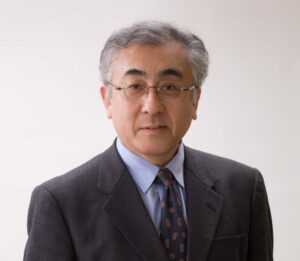
30分に3箱供給すれば良いですから、30分に①②の作業を行うと、あと10分時間が余ることになります。
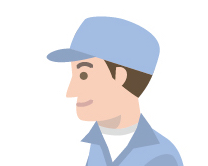
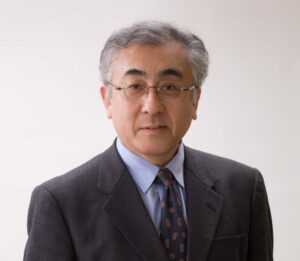
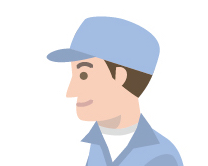
・・・やってみる
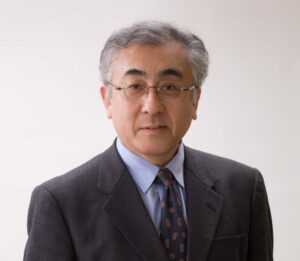
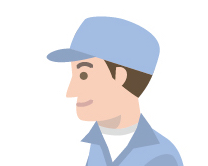
忙し気に働いていると見ていた作業も、作業を見直し、方法を設計してみると、1/3もの余裕やムダを顕在化させることができました。
この空いた1/3の時間に、価値ある仕事を割り付ける事で、この作業者の効率が上がります。
この手順を標準化し、さらには、進捗が見える管理ボード(時間軸上に、1サイクルを終えると何らかの記録を残す)を工夫し、見える化すると、異常への対応が出来、改善も進んでいきます。
作業の設計が行えていない組織には、是非とも、一歩進めて欲しいものです。